Production Philosophy
Generating value by creating processes to optimize resource utilization
Sobha Facades Touch
At the Sobha Group, we believe that there is constant room for continuous improvement and innovation. Herein lies the foundation of our lean management philosophy. As a manufacturer, we take pride in recognizing value in the entire production process, be it quality, quantity, or client satisfaction. It is entirely short-sighted to only focus on generating revenue or keeping high-profit margins.
With our pioneering Lean Management principles, we drive every business decision from the mindset of continuously raising the bar. We continue to challenge ourselves to be innovative, analytical, and always at the forefront of bringing change. This is how we keep complacency away and continue to be market leaders in the facade industry.
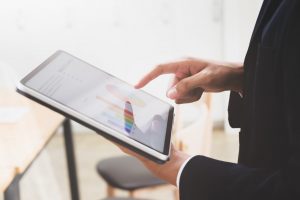
Factory on Tab
Our factory works on a ‘real-time’ approach to ensure capable planning, scheduling, and monitoring within the corresponding technology framework.
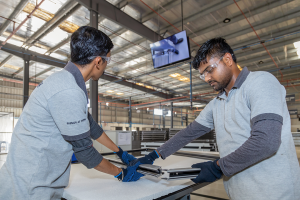
Digital Training
Enforcing a philosophy of ‘theory comes to practice’ through innovative SOPs, thereby overcoming the obstacles posed by manual SOPs.
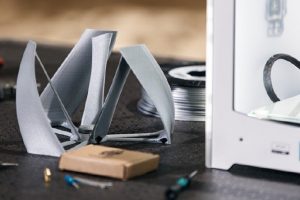
3D Prototyping
To ensure each product is precise, without any design flaws, we use modern 3D conception software and 3D printing technology for detailed prototyping.
LASTING VALUE FROM LEAN MANAGEMENT
Our lean management implementation enables us to identify value as perceived by the client. A repeatable process ensures we are able to provide our clients with consistent, custom made products that are made with their needs in mind. Sobha Facades is the culmination of an effort by a workforce that continually re-evaluates standard industry processes to increase efficiency and decrease wastage.
Best Practices
ENGINEER-TO ORDER
At Sobha Facades, we have redefined the concept of project manufacturing by putting IoT into practice. By examining the scheduling, sequencing, and resource pooling operations required for project manufacturing, a method automating the creation of a schedule based on the critical path was derived. This integrates the manufacturing schedule with the rest of the project timeline, giving greater control through every phase.
CELLULAR LAYOUT
Our cellular approach moved resources needed for a product family into a factory within the core factory, eliminating travel by 46%. This also resulted in improved communication between the various machines, better time management, and a reduced possibility of information and product families falling ‘between the cracks.’
DIGITAL INNOVATION TO TRANSFORM OPERATIONS
Digital innovation and operations management discipline is a powerful combination that boosts performance to a greater scale than previously possible. It is crucial to seize the digital moment to optimize operations management.
At Sobha Facades, technological advances are making management of operations increasingly effective. Continually updated dashboards ensure workloads are adjusted instantly, while automated data analysis allows managers to spend more time with their teams.
CAPABILITY BUILDING
The transformation of an organization at optimum speed and scale is critically dependent on team members contributing to their full potential. Our process of presenting Kaizen in front of a plant-wide group increases employee motivation and allows us to innovate further and streamline our processes. This ‘Kaizen Mela’ event has been instrumental in assisting Sobha Facade’s collective growth potential.